Spawanie laserowe
W ostatnich latach, dzięki szybkiemu rozwojowi nowej branży energetycznej, spawanie laserowe szybko przeniknęło do całej nowej energetyki ze względu na jej szybkie i stabilne zalety.Wśród nich urządzenia do spawania laserowego stanowią najwyższy odsetek zastosowań w całej nowej energetyce.
Spawanie laserowe szybko stało się pierwszym wyborem we wszystkich dziedzinach życia ze względu na dużą prędkość, dużą głębokość i małe odkształcenia.Od zgrzein punktowych po spoiny doczołowe, napawania i spoiny uszczelniające, spawanie laserowe zapewnia niezrównaną precyzję i kontrolę.Odgrywa ważną rolę w produkcji przemysłowej i wytwórczej, w tym w przemyśle wojskowym, opiece medycznej, lotniczym, kosmicznym, częściach samochodowych 3C, blachach mechanicznych, nowej energii i innych gałęziach przemysłu.
W porównaniu z innymi technologiami spawania, spawanie laserowe ma swoje unikalne zalety i wady.
Korzyść:
1. Duża prędkość, duża głębokość i małe odkształcenie.
2. Spawanie można wykonywać w normalnej temperaturze lub w specjalnych warunkach, a sprzęt spawalniczy jest prosty.Na przykład wiązka lasera nie dryfuje w polu elektromagnetycznym.Lasery mogą spawać w próżni, powietrzu lub określonych środowiskach gazowych, a także spawać materiały przechodzące przez szkło lub przezroczyste dla wiązki lasera.
3. Może spawać materiały ogniotrwałe, takie jak tytan i kwarc, a także spawać materiały różne z dobrymi wynikami.
4. Po skupieniu lasera gęstość mocy jest wysoka.Współczynnik kształtu może osiągnąć 5:1, a podczas spawania urządzeń o dużej mocy może osiągnąć nawet 10:1.
5. Można wykonać mikrospawanie.Po skupieniu wiązki lasera można uzyskać małą plamkę, którą można dokładnie ustawić.Można go zastosować do montażu i spawania mikro i małych detali w celu uzyskania zautomatyzowanej produkcji masowej.
6. Może spawać trudno dostępne miejsca i wykonywać bezdotykowe spawanie na duże odległości, z dużą elastycznością.Zwłaszcza w ostatnich latach technologia obróbki laserowej YAG przyjęła technologię transmisji światłowodowej, co umożliwiło szerszą promocję i zastosowanie technologii spawania laserowego.
7. Wiązkę lasera można łatwo rozdzielić w czasie i przestrzeni, a wiele wiązek można przetwarzać w wielu miejscach jednocześnie, zapewniając warunki do bardziej precyzyjnego spawania.
Wada:
1. Wymagana jest wysoka dokładność montażu przedmiotu obrabianego i nie można znacząco odbiegać od położenia belki na przedmiocie obrabianym.Dzieje się tak dlatego, że rozmiar plamki lasera po ogniskowaniu jest mały, a spoina jest wąska, co utrudnia dodawanie spoiwa.Jeśli dokładność montażu przedmiotu obrabianego lub dokładność pozycjonowania belki nie spełnia wymagań, istnieje ryzyko wystąpienia wad spawalniczych.
2. Koszt laserów i powiązanych systemów jest wysoki, a jednorazowa inwestycja duża.
Typowe wady spawania laserowego w produkcji baterii litowych
1. Porowatość spawania
Typowymi wadami spawania laserowego są pory.Jeziorko stopionego spawania jest głębokie i wąskie.Podczas procesu spawania laserowego azot przedostaje się do jeziorka stopionego z zewnątrz.Podczas procesu chłodzenia i krzepnięcia metalu rozpuszczalność azotu maleje wraz ze spadkiem temperatury.Kiedy stopiony metal basenowy ostygnie i zacznie krystalizować, rozpuszczalność gwałtownie i nagle spadnie.W tym czasie duża ilość gazu wytrąci się, tworząc pęcherzyki.Jeśli prędkość pływania pęcherzyków jest mniejsza niż prędkość krystalizacji metalu, powstaną pory.
W zastosowaniach w branży akumulatorów litowych często stwierdzamy, że pory powstają szczególnie często podczas spawania elektrody dodatniej, ale rzadko pojawiają się podczas spawania elektrody ujemnej.Dzieje się tak dlatego, że elektroda dodatnia jest wykonana z aluminium, a elektroda ujemna z miedzi.Podczas spawania ciekłe aluminium na powierzchni skrapla się, zanim wewnętrzny gaz całkowicie się przepełni, zapobiegając przelaniu się gazu i tworzeniu dużych i małych otworów.Małe szparki.
Oprócz wymienionych powyżej przyczyn powstawania porów, pory obejmują również powietrze zewnętrzne, wilgoć, olej powierzchniowy itp. Ponadto kierunek i kąt nadmuchu azotu również będą miały wpływ na powstawanie porów.
A jak ograniczyć występowanie porów spawalniczych?
Po pierwsze, przed spawaniem należy na czas usunąć plamy oleju i zanieczyszczenia na powierzchni przychodzących materiałów;przy produkcji baterii litowych kontrola materiałów przychodzących jest procesem niezbędnym.
Po drugie, przepływ gazu osłonowego powinien być dostosowany do takich czynników jak prędkość spawania, moc, pozycja itp. i nie powinien być ani za duży, ani za mały.Nacisk płaszcza ochronnego należy dostosować w zależności od takich czynników, jak moc lasera i położenie ogniska, i nie powinien być ani za wysoki, ani za niski.Kształt dyszy płaszcza ochronnego należy dostosować do kształtu, kierunku i innych czynników spoiny, tak aby płaszcz ochronny równomiernie pokrywał obszar spawania.
Po trzecie, kontroluj temperaturę, wilgotność i kurz w powietrzu w warsztacie.Temperatura i wilgotność otoczenia będą miały wpływ na zawartość wilgoci na powierzchni podłoża i gazu ochronnego, co z kolei będzie miało wpływ na wytwarzanie i ucieczkę pary wodnej w roztopionym jeziorku.Jeżeli temperatura i wilgotność otoczenia będą zbyt wysokie, na powierzchni podłoża i gazu ochronnego będzie za dużo wilgoci, co spowoduje wytworzenie się dużej ilości pary wodnej, w wyniku czego powstaną pory.Jeżeli temperatura i wilgotność otoczenia będą zbyt niskie, na powierzchni podłoża i w gazie osłonowym będzie za mało wilgoci, co ograniczy powstawanie pary wodnej, a tym samym zawężenie porów;pozwól personelowi ds. jakości wykryć docelową wartość temperatury, wilgotności i pyłu na stanowisku spawalniczym.
Po czwarte, metodę odchylania wiązki stosuje się w celu zmniejszenia lub wyeliminowania porów podczas spawania laserowego z głęboką penetracją.Ruch posuwisto-zwrotny belki do szwu spawalniczego powoduje wielokrotne przetapianie części szwu spawalniczego, co wydłuża czas przebywania ciekłego metalu w jeziorku spawalniczym.Jednocześnie ugięcie belki zwiększa również dopływ ciepła na jednostkę powierzchni.Zmniejsza się stosunek głębokości do szerokości spoiny, co sprzyja powstawaniu pęcherzy, eliminując tym samym pory.Z drugiej strony wahanie belki powoduje odpowiednie kołysanie małego otworu, co może również zapewnić siłę mieszania jeziorka spawalniczego, zwiększyć konwekcję i mieszanie jeziorka spawalniczego oraz korzystnie wpłynąć na eliminację porów.
Po piąte, częstotliwość impulsów, częstotliwość impulsów odnosi się do liczby impulsów emitowanych przez wiązkę lasera w jednostce czasu, co będzie miało wpływ na dopływ ciepła i akumulację ciepła w roztopionym jeziorze, a następnie wpłynie na pole temperatury i pole przepływu w stopionym basen.Jeśli częstotliwość impulsów jest zbyt wysoka, doprowadzi to do nadmiernego doprowadzenia ciepła do roztopionego jeziorka, powodując zbyt wysoką temperaturę roztopionego jeziorka, wytwarzając pary metalu lub inne pierwiastki lotne w wysokich temperaturach, co powoduje powstawanie porów.Jeśli częstotliwość impulsów jest zbyt niska, doprowadzi to do niewystarczającej akumulacji ciepła w roztopionym jeziorku, powodując zbyt niską temperaturę roztopionego jeziorka, ograniczając rozpuszczanie i ucieczkę gazu, co skutkuje powstawaniem porów.Ogólnie rzecz biorąc, częstotliwość impulsów powinna być wybierana w rozsądnym zakresie w zależności od grubości podłoża i mocy lasera i unikać zbyt dużej lub zbyt niskiej częstotliwości.
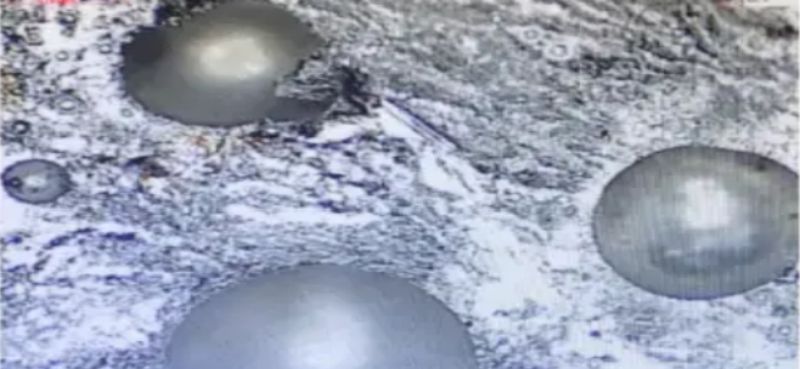
Otwory spawalnicze (spawanie laserowe)
2. Odpryski spawalnicze
Odpryski powstałe podczas procesu spawania i spawania laserowego poważnie wpływają na jakość powierzchni spoiny oraz zanieczyszczają i uszkadzają soczewkę.Ogólna wydajność jest następująca: po zakończeniu spawania laserowego na powierzchni materiału lub przedmiotu obrabianego pojawia się wiele cząstek metalu, które przylegają do powierzchni materiału lub przedmiotu obrabianego.Najbardziej intuicyjne działanie polega na tym, że podczas spawania w trybie galwanometru, po pewnym czasie używania soczewki ochronnej galwanometru, na powierzchni pojawią się gęste wżery, a wżery te są spowodowane odpryskami spawalniczymi.Po długim czasie łatwo jest zablokować światło i wystąpią problemy ze światłem spawalniczym, co skutkuje szeregiem problemów, takich jak zerwane spawanie i wirtualne spawanie.
Jakie są przyczyny rozprysków?
Po pierwsze, gęstość mocy, im większa gęstość mocy, tym łatwiej jest wygenerować rozpryski, a rozpryski są bezpośrednio powiązane z gęstością mocy.To problem mający stulecia.Przynajmniej na razie branża nie jest w stanie rozwiązać problemu rozprysków i może jedynie powiedzieć, że został on nieznacznie ograniczony.W branży baterii litowych rozpryskiwanie jest największą przyczyną zwarć baterii, ale nie jest w stanie rozwiązać pierwotnej przyczyny.Wpływ odprysków na akumulator można ograniczyć jedynie z punktu widzenia ochrony.Na przykład wokół części spawanej dodano okrąg otworów odpylających i osłon ochronnych, a także dodano rzędy noży powietrznych w okręgach, aby zapobiec wpływowi odprysków, a nawet uszkodzeniu akumulatora.Można powiedzieć, że niszczenie środowiska, produktów i komponentów wokół stanowiska spawalniczego wyczerpało dostępne środki.
Jeśli chodzi o rozwiązanie problemu odprysków, można tylko powiedzieć, że zmniejszenie energii spawania pomaga zredukować odpryski.Zmniejszenie prędkości spawania może również pomóc, jeśli penetracja jest niewystarczająca.Ale w przypadku niektórych specjalnych wymagań procesowych ma to niewielki wpływ.Jest to ten sam proces, różne maszyny i różne partie materiałów dają zupełnie inne efekty spawania.Dlatego w nowej energetyce obowiązuje niepisana zasada, jeden zestaw parametrów spawania dla jednego urządzenia.
Po drugie, jeśli powierzchnia obrabianego materiału lub przedmiotu nie zostanie oczyszczona, plamy oleju lub zanieczyszczenia również spowodują poważne rozpryski.W tym momencie najłatwiej jest oczyścić powierzchnię obrabianego materiału.
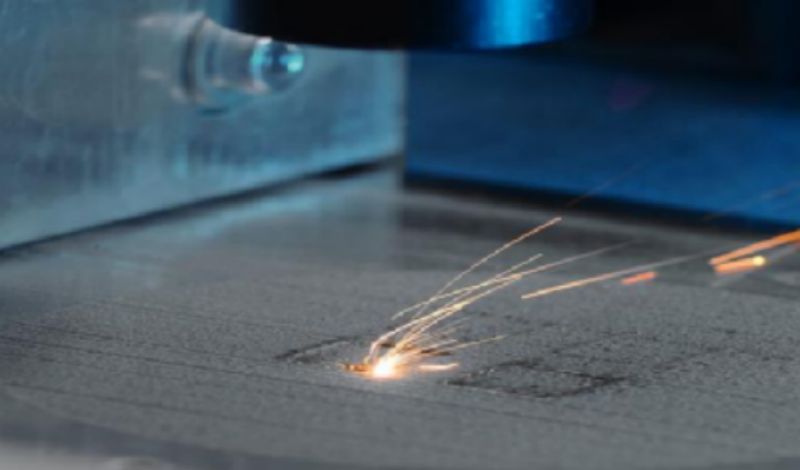
3. Wysoki współczynnik odbicia spawania laserowego
Ogólnie rzecz biorąc, wysokie odbicie odnosi się do faktu, że przetwarzany materiał ma małą oporność, stosunkowo gładką powierzchnię i niski współczynnik absorpcji w przypadku laserów bliskiej podczerwieni, co prowadzi do dużej emisji lasera, a także dlatego, że większość laserów jest używana w pionie Ze względu na materiał lub niewielkie nachylenie powracające światło lasera ponownie trafia do głowicy wyjściowej, a nawet część powracającego światła jest wprowadzana do światłowodu przenoszącego energię i przekazywana z powrotem wzdłuż światłowodu do wnętrza lasera, dzięki czemu podstawowe elementy wewnątrz lasera nadal mają wysoką temperaturę.
Jeżeli współczynnik odbicia jest zbyt wysoki podczas spawania laserowego, można zastosować następujące rozwiązania:
3.1 Użyj powłoki przeciwodblaskowej lub potraktuj powierzchnię materiału: pokrycie powierzchni materiału spawalniczego powłoką przeciwodblaskową może skutecznie zmniejszyć współczynnik odbicia lasera.Powłoka ta jest zwykle specjalnym materiałem optycznym o niskim współczynniku odbicia, który pochłania energię lasera zamiast ją odbijać.W niektórych procesach, takich jak spawanie kolektora prądu, łączenie miękkie itp., powierzchnia może być również wytłaczana.
3.2 Regulacja kąta spawania: Regulując kąt spawania, wiązka lasera może padać na spawany materiał pod bardziej odpowiednim kątem i ograniczać występowanie odbić.Zwykle dobrym sposobem na redukcję odbić jest ustawienie wiązki lasera prostopadle do powierzchni spawanego materiału.
3.3 Dodawanie absorbentu pomocniczego: Podczas procesu spawania do spoiny dodaje się pewną ilość absorbentu pomocniczego, takiego jak proszek lub płyn.Absorbery te pochłaniają energię lasera i zmniejszają współczynnik odbicia.Należy wybrać odpowiedni pochłaniacz w oparciu o konkretne materiały spawalnicze i scenariusze zastosowania.W branży baterii litowych jest to mało prawdopodobne.
3.4 Użyj światłowodu do transmisji lasera: Jeśli to możliwe, do transmisji lasera do pozycji spawania można użyć światłowodu, aby zmniejszyć współczynnik odbicia.Światłowody mogą kierować wiązkę lasera do obszaru spawania, aby uniknąć bezpośredniego narażenia na powierzchnię spawanego materiału i ograniczyć występowanie odbić.
3.5 Dostosowywanie parametrów lasera: Dostosowując parametry, takie jak moc lasera, długość ogniskowej i średnica ogniskowej, można kontrolować rozkład energii lasera i redukować odbicia.W przypadku niektórych materiałów odblaskowych zmniejszenie mocy lasera może być skutecznym sposobem ograniczenia odbić.
3.6 Użyj rozdzielacza wiązki: Rozdzielacz wiązki może skierować część energii lasera do urządzenia absorpcyjnego, zmniejszając w ten sposób występowanie odbić.Urządzenia rozdzielające wiązkę składają się zwykle z elementów optycznych i absorberów, a dobierając odpowiednie elementy i dopasowując układ urządzenia, można uzyskać niższy współczynnik odbicia.
4. Podcięcie spawalnicze
Które procesy w procesie produkcji baterii litowych z większym prawdopodobieństwem powodują podcięcie cenowe?Dlaczego dochodzi do podcięcia cenowego?Przeanalizujmy to.
Podcięcie, generalnie surowce spawalnicze nie są dobrze ze sobą połączone, szczelina jest zbyt duża lub pojawia się rowek, głębokość i szerokość są zasadniczo większe niż 0,5 mm, długość całkowita jest większa niż 10% długości spoiny lub większa niż standard procesu produktu o żądaną długość.
W całym procesie produkcji baterii litowej prawdopodobieństwo wystąpienia podcięcia jest bardziej prawdopodobne i jest ono zwykle rozprowadzane podczas wstępnego spawania uszczelniającego i spawania cylindrycznej płyty pokrywy oraz wstępnego spawania i spawania uszczelniającego kwadratowej aluminiowej płyty pokrywy.Głównym powodem jest to, że pokrywa uszczelniająca musi współpracować z płaszczem podczas spawania, proces dopasowywania pomiędzy płytą uszczelniającą a płaszczem jest podatny na nadmierne szczeliny spawalnicze, rowki, zapadnięcia itp., Dlatego jest szczególnie podatny na podcięcia .
Co zatem powoduje podcięcie cenowe?
Jeśli prędkość spawania jest zbyt duża, ciekły metal za małym otworem skierowanym na środek spoiny nie będzie miał czasu na ponowne rozprowadzenie, co spowoduje zestalenie i podcięcie po obu stronach spoiny.W związku z powyższą sytuacją konieczna jest optymalizacja parametrów spawania.Mówiąc najprościej, jest to powtarzanie eksperymentów w celu sprawdzenia różnych parametrów i kontynuowanie DOE, aż do znalezienia odpowiednich parametrów.
2. Nadmierne szczeliny, rowki, zapadnięcia itp. materiałów spawalniczych zmniejszą ilość stopionego metalu wypełniającego szczeliny, zwiększając prawdopodobieństwo wystąpienia podcięć.To kwestia sprzętu i surowców.Czy surowce spawalnicze spełniają wymagania materiałowe naszego procesu, czy dokładność sprzętu spełnia wymagania itp. Normalną praktyką jest ciągłe torturowanie i bicie dostawców i osób odpowiedzialnych za sprzęt.
3. Jeśli pod koniec spawania laserowego energia spadnie zbyt szybko, mały otwór może się zapaść, co spowoduje lokalne podcięcie.Prawidłowe dopasowanie mocy i prędkości może skutecznie zapobiegać powstawaniu podcięć.Jak mówi stare powiedzenie, powtarzaj eksperymenty, sprawdzaj różne parametry i kontynuuj DOE, aż znajdziesz właściwe parametry.
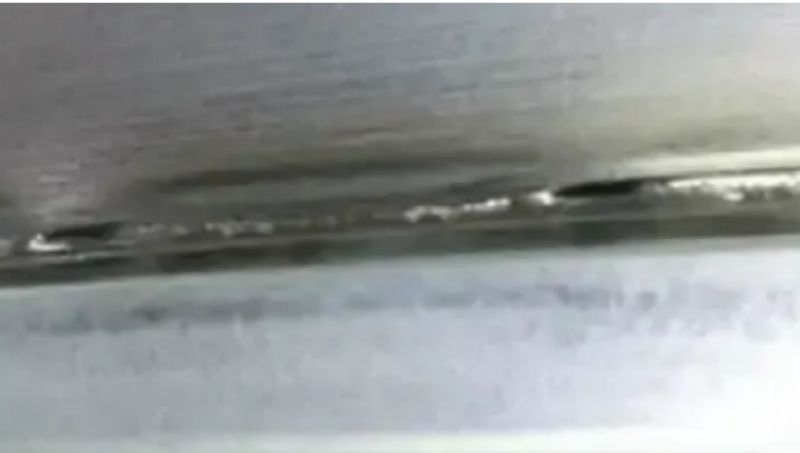
5. Zapadnięcie się środka spoiny
Jeśli prędkość spawania jest mała, jeziorko stopionego będzie większe i szersze, zwiększając ilość stopionego metalu.Może to utrudniać utrzymanie napięcia powierzchniowego.Kiedy roztopiony metal stanie się zbyt ciężki, środek spoiny może zagłębić się, tworząc zagłębienia i wgłębienia.W takim przypadku należy odpowiednio zmniejszyć gęstość energii, aby zapobiec zapadaniu się jeziorka stopionego materiału.
W innej sytuacji szczelina spawalnicza po prostu zapada się, nie powodując perforacji.Jest to niewątpliwie problem dopasowania wciskowego sprzętu.
Właściwe zrozumienie defektów, które mogą wystąpić podczas spawania laserowego oraz przyczyn różnych defektów, pozwala na bardziej ukierunkowane podejście do rozwiązywania wszelkich nietypowych problemów spawalniczych.
6. Pęknięcia spoin
Pęknięcia pojawiające się podczas ciągłego spawania laserowego to głównie pęknięcia termiczne, takie jak pęknięcia krystaliczne i pęknięcia upłynniające.Główną przyczyną tych pęknięć są duże siły skurczu generowane przez spoinę przed jej całkowitym zestaleniem.
Istnieją również następujące przyczyny pęknięć podczas spawania laserowego:
1. Nierozsądny projekt spoiny: Niewłaściwe zaprojektowanie geometrii i rozmiaru spoiny może spowodować koncentrację naprężeń spawalniczych, powodując w ten sposób pęknięcia.Rozwiązaniem jest optymalizacja projektu spoiny, aby uniknąć koncentracji naprężeń spawalniczych.Można zastosować odpowiednie spoiny offsetowe, zmienić kształt spoiny itp.
2. Niedopasowanie parametrów spawania: Niewłaściwy dobór parametrów spawania, np. zbyt duża prędkość spawania, zbyt duża moc itp. może doprowadzić do nierównomiernych zmian temperatury w obszarze spawania, czego skutkiem będą duże naprężenia spawalnicze i pęknięcia.Rozwiązaniem jest dostosowanie parametrów spawania do konkretnego materiału i warunków spawania.
3. Złe przygotowanie powierzchni spawania: Brak odpowiedniego oczyszczenia i wstępnej obróbki powierzchni spawania przed spawaniem, np. usunięcia tlenków, tłuszczu itp., wpłynie na jakość i wytrzymałość spoiny i łatwo doprowadzi do pęknięć.Rozwiązaniem jest odpowiednie oczyszczenie i przygotowanie powierzchni spawania, aby zapewnić skuteczne usunięcie zanieczyszczeń i zanieczyszczeń w obszarze spawania.
4. Niewłaściwa kontrola dopływu ciepła spawania: Zła kontrola dopływu ciepła podczas spawania, np. nadmierna temperatura podczas spawania, niewłaściwa szybkość chłodzenia warstwy spawalniczej itp., doprowadzi do zmian w strukturze obszaru spawania, czego efektem będą pęknięcia .Rozwiązaniem jest kontrolowanie temperatury i szybkości chłodzenia podczas spawania, aby uniknąć przegrzania i szybkiego ochłodzenia.
5. Niewystarczające odprężanie: Niewystarczające odprężanie po spawaniu spowoduje niewystarczające odprężenie w spawanym obszarze, co łatwo doprowadzi do pęknięć.Rozwiązaniem jest wykonanie odpowiedniej obróbki odprężającej po spawaniu, takiej jak obróbka cieplna lub obróbka wibracyjna (główny powód).
Jeśli chodzi o proces produkcji baterii litowych, które procesy częściej powodują pęknięcia?
Ogólnie rzecz biorąc, pęknięcia są podatne na powstawanie pęknięć podczas zgrzewania uszczelniającego, np. zgrzewania cylindrycznych osłon stalowych lub osłon aluminiowych, zgrzewania uszczelniającego kwadratowych osłon aluminiowych itp. Ponadto podczas procesu pakowania modułów podatne jest również spawanie odbieraka prądu do pęknięć.
Oczywiście możemy również zastosować drut wypełniający, podgrzewanie lub inne metody, aby zmniejszyć lub wyeliminować te pęknięcia.
Czas publikacji: 01 września 2023 r